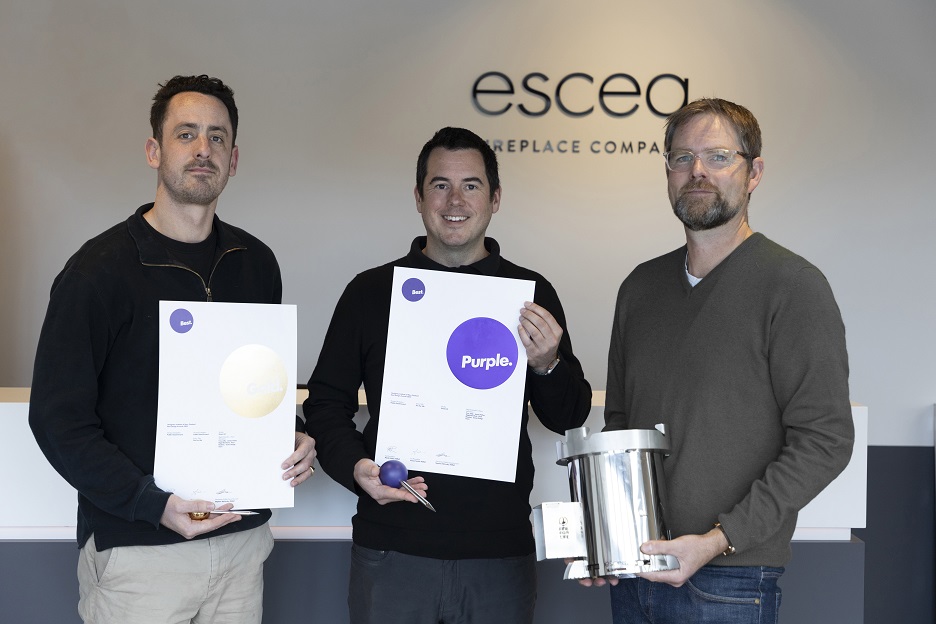
The fireplace designer and manufacturer won three awards at the New Zealand Best Design Awards, held by the Designers Institute of New Zealand in Auckland recently
The company’s not-for-profit initiative Fire for Life won the gold and prestigious purple award in the public good category and a gold award in the non-consumer product category.
Escea’s team developed a portable, lightweight stove over six years which is flat-packed in its Green Island factory and shipped to international humanitarian organisation ReliefAid to be assembled in Syria - providing income for locals - and distributed to refugees living in displacement camps.
One of the biggest issues faced by families was access to fuel, the time it took to collect it and the cost of buying it.
The aim of the project was to solve the problems of open-fire cooking in camps by supplying families with efficient stoves that were designed to use less fuel, cook faster, were transportable and produced less smoke.
Escea chief executive Nigel Bamford said the company previously won accolades for its fireplace products at the design awards but it was the first time it had entered the stove design.
It was nice to show the design community that design could be useful and make an impact, rather than simply be about "making things pretty or sell well".
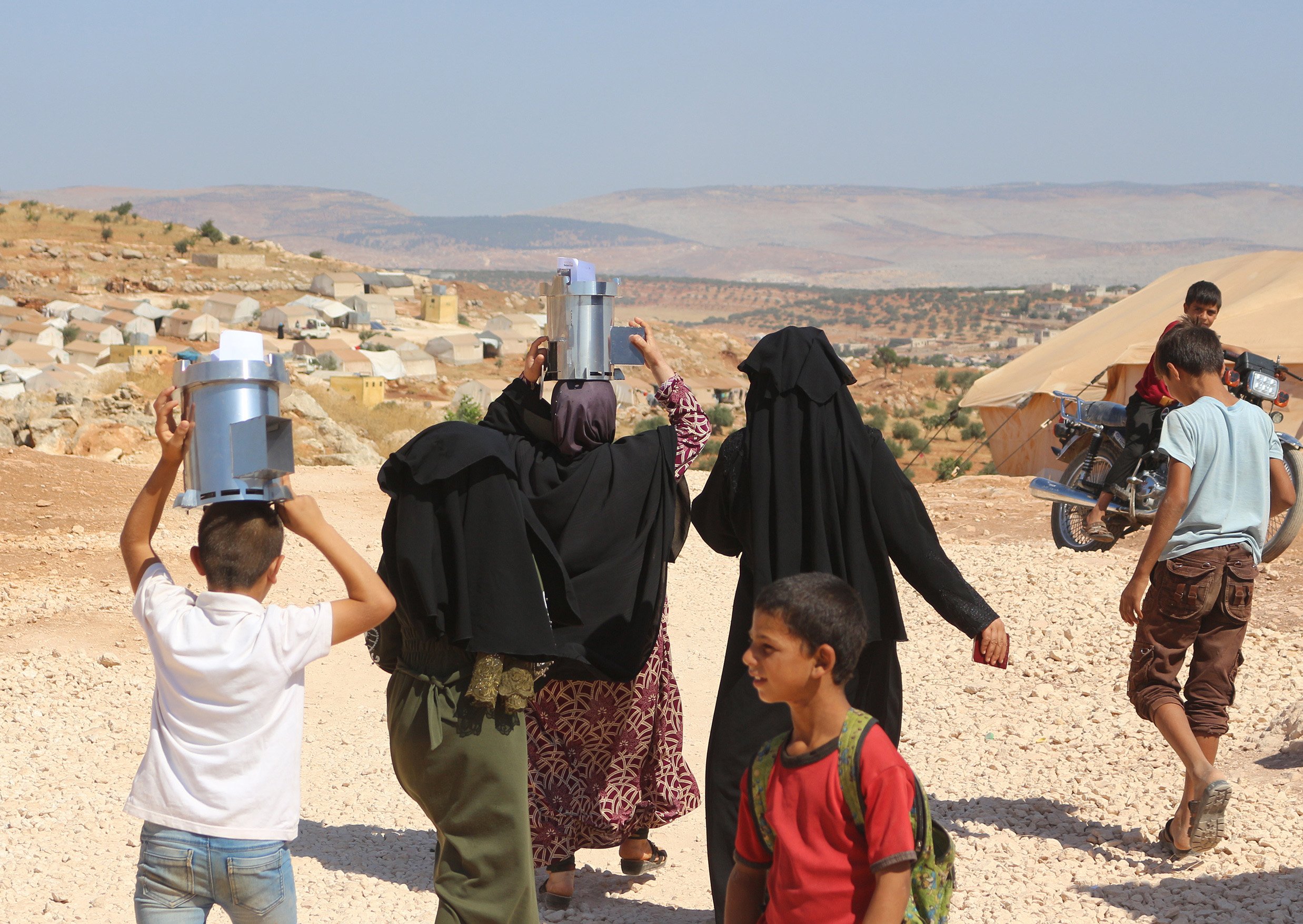
"A kitset fireplace that easily ships and assembles yet integrates generations of knowledge to channel air and create efficient burning and is all achieved from a single sheet of material.
"The project embodies great design by solving an old problem, in a novel way."
When it came to adopting a not-for-profit initiative, Escea wanted a project with maximum impact and found itself trying to help some of the poorest people in the world, Mr Bamford said.
There were 12million refugees in Syria living in displacement camps. Open fires provided warmth, light, a way to cook and drink clean water.
But the fires they used were handmade from the only resources they had access to - discarded cans, rocks, dirt and clay.
Those fires burned fast and inefficiently - they needed more firewood to burn, cooking took longer, they could not easily be moved around, were in danger of setting nearby tents on fire, and created more smoke that could be inhaled by the families using them.
The team chose a project that added value to their skill set and it had been adopted company-wide, Mr Bamford said.
The company fully funded the project to get the stoves made and distributed and partnered with ReliefAid to deliver them.
Creating a stove that could be made at a low cost and burned at twice the combustion efficiency than the existing options in the camps was one of the most challenging design tasks it had ever undertaken.
It was cut out of sheet metal using laser cutters during off-peak hours when those automated machines would otherwise not be operating.
That meant the only cost was the raw material and shipping. The flat-pack design meant 200 stoves could fit on a small pallet.
The stove used a spiral air pathway around the outside to create a vortex of flame inside.
That forced the flame to interact with more air, making it burn hotter and with less smoke - a principle used in highly efficient first-world fireplaces which had been distilled down to its simplest form.
Post-distribution surveys done through ReliefAid showed the stoves received a "very very positive response" and had a big impact on the refugees’ lives, Mr Bamford said.
Last year, 4000 stoves were dispatched to Syria and the company said the journey had only just begun.
Many more communities required support around the world.